hemming process sheet metal The sheet metal hemming process is commonly used to create metal parts with complex shapes and structures in industries including Heating, automotive, metal furniture, aerospace, and electronics. How is sheet metal .
30"W, 2-drawer steel file cabinet provides an expansive amount of space for your documents. Putty steel lateral file cabinet blends in seamlessly with most office environments. Eco-conscious choice — has one or more meaningful eco-attributes or eco-labels.
0 · types of sheet metal seams
1 · sheet metal hem design guide
2 · sheet metal hand hemming tool
3 · seaming process in sheet metal
4 · seam joint in sheet metal
5 · open hem sheet metal
6 · hemmed edge sheet metal
7 · hem300 vs hem305
High-performance, affordable American-Made Thermwood CNC Routers are used in Wood, Plastics, Aerospace, Composites, Foam, Non-Ferrous Metals & now additive with the LSAM Large Scale Additive Manufacturing System.We manufacturer CNC woodworking machines built in the USA with all-steel frames that come fully assembled and pre-tested. We provide the industry’s best customer service and training.
Hemming in sheet metal operations refers to the bending of a sheet metaledge onto itself. It is very similar to edge stitching in clothes. Similar to how an edge stitch strengthens the edge and makes it more durable, a hem imparts strength to the metal edge and improves its appearance. The edge of one part may . See more

The hemming process can be carried out in one of the following two ways: 1. Die hemming process 2. Roller hemming process See moreA seam is used to connect two metal parts by interlocking the edges of the folded sheet metal parts. The resulting shape may even form a . See more
Sheet metal hemming is a manufacturing process that folds metal edges to reinforce strength and safety. It reduces sharpness and enhances aesthetics, often used in .
Explore how the sheet metal hemming process improves the structural integrity of sheet metal parts. Learn about hem types and their applications. The sheet metal hemming process is commonly used to create metal parts with complex shapes and structures in industries including Heating, automotive, metal furniture, aerospace, and electronics. How is sheet metal . In sheet metal fabrication, the hemming process involves bending the same part’s sharp edges to form a reinforcement channel. This process is widely used across the automotive and electronics industries. It cuts thin sheet .
Hemming and seaming are two similar metalworking processes in which a sheet metal edge is rolled over onto itself. Hemming is the process in which the edge is rolled flush to itself, while a .Sheet metal hemming is a unique technique that involves folding the edge of sheet metal back on itself to create a double thickness. This process adds durability and strength to the part but eliminates sharp edges. It ensures .Sheet Metal Hemming Vs. Sheet Metal Seaming. The rolling over of a sheet metal edge onto itself is known as hemming in the metalworking industry. Hemming includes rolling the edge flush against itself instead of sewing, which joins the .
As we mentioned above, sheet metal hemming is a process of folding the edge of a single metal sheet back onto itself to create a clean, finished edge. This is typically done by bending the .August 31, 2024. Contents. Struggling with sheet metal edges issues? Hemming is the solution. Rough edges not only look unprofessional but can also be harmful. This important technique makes safe, smooth and durable edges for different . Sheet metal hemming is a vital process in metal fabrication, providing enhanced strength, aesthetics, and functionality to metal components. By understanding the technology, techniques, and applications of hemming, manufacturers can make informed decisions that lead to high-quality results. Whether you are in the automotive industry, appliance . The process, called hole hemming, involves deforming the metal sheet to establish a mechanical interlock with the polymer sheet, requiring neither heating nor auxiliary elements. The applicability of this process is tested for joining aluminum and polycarbonate (PC) sheets.
Hemming suits only high-gauge sheet metal (thinner sheets <=0.125”). Low-gauge sheets (thicker sheets) are prone to fracturing on bending. How Sheet Metal Hemming Works. Sheet metal hemming is a multi-step .In hemming, the sheet-metal parts are bent in a forming process and then positively joined by welding or brazing. Firstly, the edge of the sheet metal is bent over. The component is stiffened and can subsequently be joined. Hemming is also capable of joining different components.
types of sheet metal seams
Here are the benefits of this process: Sheet Metal Hemming – Aesthetic improvements. Applying a hemming procedure on your sheet metal materials can help improve the aesthetics of the final product. Hemming edges are even more tidy compared to the un-hemmed edges. Better-looking edges will increase the overall value of your sheet metal products.The Sheet Metal Hem Process: A Step-by-Step Guide. After the preparation is complete, the heart of the procedure is the sheet metal hemming. To ensure quality and consistency, our team follows a step-by-step process. Bending and folding Techniques. When to apply the 4 Common Types of Sheet Metal Hems to your Design 1. Closed hem. Also known as a crushed hem, a closed hem is completely flush (as opposed to an open hem, which allows for a bit of space in the bend).. Closed hems are the most popular type of hem because they’re so easy to make: the sheet metal is simply flattened onto itself.As we mentioned above, sheet metal hemming is a process of folding the edge of a single metal sheet back onto itself to create a clean, finished edge. This is typically done by bending the metal over a die or roller, resulting in a 180-degree fold or a tighter, more acute angle. Hemming provides a smooth, rounded edge that is less prone to .
cnc engineering machine
In the manufacturing industry, the sheet metal process is common, and sheet metal parts are used in many different industries, including consumer products, appliances, aircraft, and the automotive and aerospace sectors. Sheet Metal Operations. Following are the 9 different types of sheet metal operations: Shearing Operations; Blanking Operations The conditions and rules for press brake forming hems on sheet metal. Learn more at https://www.allmetalsfab.comHemming is a common sheet metal technique use.
Depending on the material and your tool set-up, you can hem sheet metal up to 4mm thick. Check out our product specifications or contact WILA for advice. . Our hydraulic Dutch bending tables can be used for automating the hemming process. Contact WILA to explore your options.
cnc engraving machine with multi-spindles
sheet metal hem design guide
Welcome to Kreatorzone! On this sheet metal design series you will find the recommended Common sheet metal design guidelines in Hem Feature Guidelines or Hem.In sheet metal hemming means to fold the metal back on itself. When working with a Brake Press hems are always created in a two step process: Create a bend with Acute Angle Tooling in the metal, 30° is preferable but 45° will work for some circumstances. Hemming is a sheet metal forming process in which sheets are joined by bending it usually to 180°. Automotive body panels and automotive parts such as deck-lids, trunk-lids, doors, hoods and tailgates are formed by hemming process. This paper present a systematic review of sheet metal hemming process based on materials used in hemming process .

Metal hemming is a vital process in the field of sheet metal fabrication and manufacturing. It involves bending, folding, or curling the edge of a metal sheet to create a secure, finished, and aesthetically pleasing joint.
As we mentioned above, sheet metal hemming is a process of folding the edge of a single metal sheet back onto itself to create a clean, finished edge. This is typically done by bending the metal over a die or roller, resulting in a 180-degree fold or a tighter, more acute angle. Hemming provides a smooth, rounded edge that is less prone to . Hemming is a sheet metal forming process in which sheets are joined by bending it usually to 180 . Automotive body panels and automotive parts such as deck-lids, trunk-lids, doors, hoods and . Sheet metal hemming is a multi-step process that makes strong, smooth edges. First, the metal sheet is cut to size and the edge is bent at a 90-degree angle. Next, the bent edge is folded back onto itself at a 180-degree angle. It makes a double layer of metal along the edge. The folded edge is then flattened by using particular tools or machines.
As we mentioned above, sheet metal hemming is a process of folding the edge of a single metal sheet back onto itself to create a clean, finished edge. This is typically done by bending the metal over a die or roller, resulting in a 180-degree fold or a tighter, more acute angle. Hemming provides a smooth, rounded edge that is less prone to .
In this study, the fracture problem occurring in the bending areas of the sheet metal panel produced by the hemming process was investigated by numeri.As we mentioned above, sheet metal hemming is a process of folding the edge of a single metal sheet back onto itself to create a clean, finished edge. This is typically done by bending the metal over a die or roller, resulting in a 180-degree fold or a tighter, more acute angle. Hemming provides a smooth, rounded edge that is less prone to .
The whole process is characterised by a 90° sheet flanging, a pre-hemming (up to approximately 135°) and the final hemming where the outer sheet edge is bended up to 180° clamping the inner sheet.As we mentioned above, sheet metal hemming is a process of folding the edge of a single metal sheet back onto itself to create a clean, finished edge. This is typically done by bending the metal over a die or roller, resulting in a 180-degree fold or a tighter, more acute angle. Hemming provides a smooth, rounded edge that is less prone to . Common sheet metal design guidelines in Hem Feature Guidelines or Hemming sheet metal process; Final Summary: Unleashing the Power of the Hemming Tool in Sheet Metal Fabrication; When it comes to sheet metal fabrication, having the right tools can make all the difference. One such tool that is essential for achieving precise and professional . Hemming is a crucial process in sheet metal fabrication, particularly for creating safe, durable, and aesthetically pleasing edges. It involves folding the edge of a piece of sheet metal back onto .
sheet metal hand hemming tool
Abstract. Hemming is a material processing technology widely used in major sectors such as automotive and aerospace industries. As a mechanical joining process, hemming is applied to sheet metal components to build structural assemblies. In conventional hemming methods, dies and presses are used by designing product-specific tooling. In recent years, . 12.Hemming: It is an operation in which the edge of the sheet is folded over itself. This process increases stiffness of the part and eliminate sharp edges. RIT - M.Lakshmanan, AP (S.G)/MECH 70 . When the forming process the sheet metal and tooling are heated together and then high pressure of gas is applied. That case, the sheet metals are .
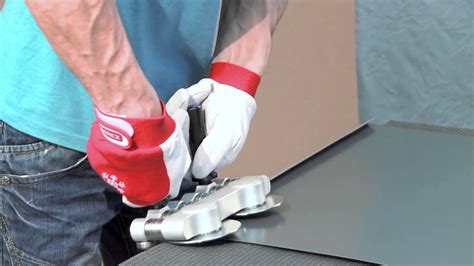
Check out our wood and metal urn selection for the very best in unique or custom, handmade pieces from our caskets & urns shops.
hemming process sheet metal|sheet metal hem design guide