welding two continuous sheet metal Welding a continuous edge on a sheet metal box . Illustration here for reference. . I made the base geometry easily by converting a solid to sheet metal but I cannot seem to draw a weld bead along the continuous edge which includes the chamfer. Selecting one face will not chain the adjacent ones and will not create a weld bead against the . Get information, directions, products, services, phone numbers, and reviews on Trenton Sheet Metal in Trenton, undefined Discover more Fabricated Plate Work (Boiler Shops) companies in Trenton on Manta.com
0 · welding sheet metal corners
1 · welding aluminum sheet metal
2 · sheet metal welding process
3 · sheet metal welding parts
4 · sheet metal welding methods
5 · sheet metal welding guide pdf
6 · metal welding sheet metal
7 · intermittent welding sheet metal
The company offers its expertise for exhaust/fume collection systems and HVAC ductwork. Some of the services offered include sheet metal/plate manufacturing, welding, bending, shearing, rolling, machining, testing and on-site installation.
Each welding process requires specific precautions and equipment setup for a successful sheet metal weld. So, let’s discuss the preparation needed for each arc welding process before proceeding to the common problems with thin gauge welds. See moreNow that we’ve covered the essential considerations for different arc welding processes, let’s discuss how to prevent and fix common . See more
Welding thin metal is challenging. There is no denying that. But, if you practice and use the tips we shared in this article, you’ll get the best chance for success. After you inevitably burn through some scrap sheets of metal and warp others, you’ll gain more experience and learn . See more Seam welding, or fillet welding, is one of the most common methods we use at Approved Sheet Metal. This arc welding method uses a .
Welding a continuous edge on a sheet metal box . Illustration here for reference. . I made the base geometry easily by converting a solid to sheet metal but I cannot seem to draw a weld bead along the continuous edge which includes the chamfer. Selecting one face will not chain the adjacent ones and will not create a weld bead against the . Sheet metal welding is a process that seems relatively simple at first glance – connecting several metal parts with the help of high temperatures and filler material. However, there is a lot more to it than just this explanation, .
The most common type of weld is the butt weld, which joins two pieces of metal at their ends. A lap joint weld joins two pieces of metal that overlap each other, while a T-joint weld joins two pieces of metal at right .a series of spot welds or a continuous weld between two overlapping piece of metal. . used with sheet metal, the two curved edges are welded together. Corner- Flange Weld. like the edge but one piece is flanged. Main part of fillet weld. face leg root toe throat. Spot weld. popular for sheet metal. Under pressure the heat of the arc fuses .
1 3 Expert Weldment Techniques at Approved Sheet Metal. 1.1 Spot welding. 1.2 Seam welding. 1.3 Plug welding. 2 Weldment Best Practices at Approved Sheet Metal; 3 Sheet Metal Part Design for Manufacturing Tip. 3.1 CORNERS AND WELDING; 4 Sheet Metal Weldment Techniques FAQ. 4.0.1 What is welding, and how does it relate to historical .
MIG (Metal Inert Gas) welding, also known as Gas Metal Arc Welding (GMAW), is a welding process that uses a continuous wire electrode and a shielding gas to fuse two pieces of metal together. Image: ( Fronius ) The fact is that no matter how good or careful you are, metal WILL warp when you’re welding on sheet metal. We’ve heard all of the tricks in the book, but none of them completely stop the warping; only reduce or control it. The secret is that the heat and cooling from welding will shrink the metal around the weld seam to some degree. Sheet metal welding is done by heating two thin sheets of metal to melting point. The melted sheets are then skillfully joined together using a torch to form the desired shape and specifications. . Begin welding along the joint, moving the torch in a steady motion to create a continuous weld bead. Welding sheet metal is a very critical process within the modern concept of manufacturing. The construction of metal structures, pipelines, and tanks is among the most common applications for sheet metal welding. Though the process is rather straightforward, it can be complex to achieve quality and efficiently weld thin sheet metals. Understanding the key .
I love my Mig welders, The Mig Process is great for many types of weld repairs, but so is GAS welding and Tig welding. Just My Opinion But the Mig welding process has very little place in the world Automotive sheet metal panel Restoration world when the BEST QUALITY work and product is desired and is to be performed.

best tiawanese cnc machine
welding sheet metal corners

Sheet metal welding is at the core of a wide range of industries, from automotive to construction, playing a vital role in the production of sturdy, high-quality components. The process involves joining two pieces of metal together using heat, which melts a filler metal into the joint to create a strong bond. . #4 Continuous Training and . Sheet metal welding is a crucial manufacturing process that helps join and assemble metal structures. . forming a solid continuous bond. Sheet metal welders work in various world industries, including aerospace, automotive, marine, electronics, assembly plants, etc. . They exist in two forms: (1) Groove Weld. In grove welding, the two .
Table of Contents. 1 Spot Weld vs. Seam Weld; 2 7 Things to Know About Spot Welding ; 3 Sheet Metal Part Design for Manufacturing Tip. 3.1 CORNERS AND WELDING; 4 Spot Welding FAQ. 4.0.1 What is the difference between spot welding and seam welding, and when should I choose one over the other?; 4.0.2 What is plug welding, and when should I .The molten filler metal will flow in and fill the gap between the two base metals. Types of Sheet Metal Welding Processes. . MIG welding is an arc welding procedure that uses a continuous feed of a consumable wire electrode as the filler metal. It uses an electric current to strike an arc between the wire electrode and the base metal. Unlocking the Secrets of Lap Joints: A Welding Enthusiast’s Guide. Ah, the humble lap joint – the unsung hero of sheet metal projects! As a passionate welding enthusiast, I’m here to tell you that mastering the art of .
As a rule, when MIG welding sheet metal, never use a body filler metal that is thicker than the base metal. It is recommended that a welder should use .023- or .024-inch wire for light gauge sheet metal work.
As for welding the roll cage tube to sheet metal, couldn’t you just focus more heat to the rollcage tube and “wash over” the heat to the sheet metal? Answer: No, not in every situation. I’m still not sure why it’s a series of spot welds, other than making it look like TIG to an untrained eye, or to prevent burn through I welded up some sheet metal with my new to me MM250 with the standard .035 wire. The tack, tack, tack method worked great for me and can be fast once you get into it. This was my second actual MIG weld I done going from the sheet metal to 1/4" box tube. Continuous learning and improvement are key to mastering welding sheet metal on cars. Consider attending welding workshops, reading up-to-date materials, or watching online tutorials to enhance your understanding of welding techniques, safety measures, and .
Welding sheet metal with a flux core is feasible for thin materials. This process utilizes a flux-cored wire to shield the weld pool. . The process involves a continuous wire feed through the welding gun, which differs slightly from traditional welding methods. With the correct tools and settings, even beginners can produce high-quality work . IOOOFU Durable Car Body Repair Tool Spot Welding Dent Puller Ring-Gun Shoot Reload-Continuous Ejector with Washers Profession Black Iron. . iDili Automotive Sheet Metal Dent Quick Puller Spot Welding Pulling Unit Car Body Fine Repair Tool Small Leveling Bar Lifter (B: Large Type Gun use/Data recovery) Share:
The process involves using filler metals and heating the two components to a high enough temperature that they can fuse, creating a strong bond that will hold up over time.Additionally, the special filler material may be needed when welding certain types of sheet metal due to its unique properties. The result of successful weld thin sheet metal is a durable product that holds up .
It works very well and there is virtually zero cleanup after the process. Basically a d/a sander as with any sheet metal prior to under and top coats. Plug, and stitch welding in the same task is much more lengthy and time consuming. A 1/4 second 8000 amp instantaneous resistance spot weld is quite strong on automobile sheet metal. The two most common electrode wire diameters for sheet metal welding are 0.6mm (.023-.025 inch) and 0.8mm (.030 inch). A shielding gas is required to protect the weld puddle from atmospheric contamination during GMA (MIG) welding.
welding aluminum sheet metal
MAG welding (Metal Active Gas) is a type of Gas Metal Arc Welding (GMAW) that uses active gases, like carbon dioxide (CO2) or a mixture of CO2 and argon, to shield the weld pool. This welding process is ideal for ferrous metals, particularly mild steel, where the active gas can react with the weld pool to improve stability and penetration.The heat from the arc melts the metal, and as the wire electrode is consumed, it fills the weld joint, joining the two pieces of metal. The shielding gas protects the weld pool from contaminants, ensuring a clean and strong weld. A MIG welder refers to . To most manufacturers, spot welding is the most economical way to join two pieces of sheet metal. While joining sheet metal is the most common use for the process, resistance welding (RW) equipment actually can be used for a large variety of joining and heat-treating projects, some of which are not so well-known. Resistance Welding Annealing
best value cnc milling machine
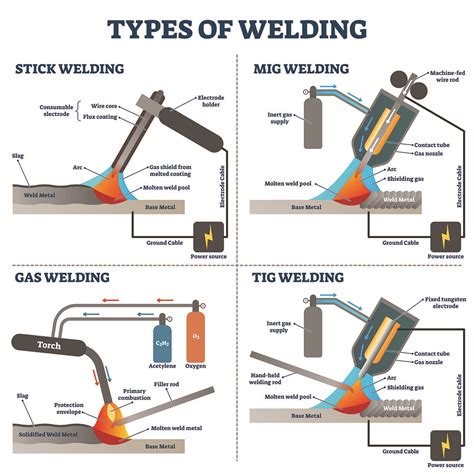
In the Trinity UFO-crash tale told by Jacques Vallee and Paola Harris in their book Trinity: The Best-Kept Secret, Eddie Apodaca is a key figure -- a "friend of the family" who actually entered the crashed alien craft on August 18, 1945.
welding two continuous sheet metal|welding sheet metal corners